Использование лазерного сканирования в конструкции насоса
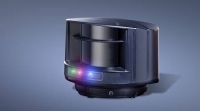
3-D лазерное сканирование является относительно новой технологией, которая дает трехмерную виртуальную запись реального объекта. Концепция проста и похожа на полицейских радаров, но требует, мощность современных компьютеров день для сбора и обработки огромного количества дискретных данных мгновенно. Основные работы лазерного сканирования включает в себя проектирование луч на объект. Оптический датчик похож на такого рода в цифровых камер записывает отражение пучка X, Y и Z координаты точки в 3-D пространстве. В итоге 3-D запись объекта интереса.
Конкурентные преимущества, которые эта технология обеспечивает один из всеобъемлющего виртуального сравнения, что позволяет компаниям источника продукт из любой точки мира быстро со 100-процентной уверенности в повторяемости.
Рассмотрим традиционные требования процессе поиска геометрически сложные отливки типичных для центробежного насоса из области низких затрат (LCR). Во-первых, 2-D чертежей отправляются в литейных для литья создания шаблона. Рисунки интерпретируются и узоров вырезает узор инструмент вручную, используя шаблоны и традиционные инструменты. Несколько отливок изготавливаются и обрабатываются для целей качества образца.
Пример части отправлены обратно на завод и каждый конкретный размер измеряется рисунок от руки и регистрируется. Из-за гидравлической производительности на первичном рынке результата, полная насосы затем построен и испытан для доказательства эффективности. Этот процесс ручной трудоемкой и традиционно требуется много месяцев, чтобы завершить успешно. Несоответствия в части геометрии может продлить сроки этого процесса еще больше.
В 21 -м веке, 3-D модель необходимой части может быть немедленно отправлено через Интернет любому поставщику в любой точке мира для производства. Литье шаблоны для гидравлической части (корпуса, рабочие колеса и т.д.), созданные с ЧПУ от 3-D модель для максимальной уверенности в геометрии детали и точности. Когда насос производитель закупает и получает эти литье, детали проверяются на 3-D лазер, а затем оценивали с помощью мощных состоянии современного программного обеспечения.
При условии, что части в течение минимум допусков, никаких дополнительных гидравлических испытаний не требуется, и они могут быть приняты к производству без многочисленных тестов производительности. С другой стороны, затраты и задержки в реализации проекта гидравлических испытаний производительности можно избежать, если есть значительная часть несоответствия вопросов в связи с изменением производства. 3-D Цвет карты несоответствия направляется поставщику для коррекции без дальнейшего промедления.
Когда насос части интерес представляют те, которые были произведены внутри страны, лазерное сканирование предполагает больший, более важную роль в этом процессе. В этом случае необходимо, чтобы любой новый инструмент совпадает с наследием инструментов, чтобы гидравлическая производительность поддерживается в разных поставщиков. В этом случае, первый шаг в процессе сканирования решающим инструментом наследия части. Эти данные сканирования, то по сравнению с предлагаемой 3-D модель, чтобы устранить любые различия между несколькими инструментами картину. Этот процесс был и продолжает быть с успехом использованы в различных проектах источников для устранения риска несколько аттестации и инструмент изменений.
Эта карта показывает отклонение цвета 3-D различия между 3-D модели и лазерное сканирование литья. Это рабочее колесо было принято без гидравлического тестирования производительности.
Этот 3-D проверки фактического литья клапан был использован клапан производителя, чтобы проверить их 3-D модель для обеспечения соответствия продукции согласованность между несколькими поставщиками.
Многие компании, которые приняли сканирования использовать его в сочетании с CAD-системами инженерии. Такое использование является естественным продолжением из-за сходства между технологиями, так как они оба живут в виртуальном 3-D пространстве. Типичные области применения можно разделить на три основные категории:
Обратное проектирование: модель CAD необходимо, но не рисунки или записи существуют. Например, сборная США Бобслей использовать сканирование, чтобы создать модель САПР драйвера для запуска компьютерного моделирования аэродинамическое сопротивление.
Обратное моделирование: троюродный брат с обратной инженерии, обратного моделирования позволяет CAD модели для проверки на фактическое участие обеспечить точность моделирования.
Компьютер Проверка: Любая часть можно сравнить с его моделью CAD для обеспечения соответствия техническим требованиям.
Лазерное сканирование может быть использовано и в других, уникальных путей улучшения процессов и продукции, которые развелись полностью из CAD-систем, основанных на технике. В отличие от типичных приложениях, эти методы основаны на анализе сканирования файлов данных только. В следующем примере мы увидим, как и почему компания использует "CAD-менее" анализа для улучшения процессов и продукции.
Улучшение литейных процессов Corebox, что создает песок ядро используется в литье небольшого рабочего колеса насоса было закуплено от внешнего магазин шаблон для замены старых инструментов. В рамках процесса квалификации производство, было обнаружено, что стержневой смеси не может быть удален из corebox, что делает инструмент бесполезно. Из-за небольшого размера corebox, традиционные методы измерения не может подтвердить обратное проект в качестве виновника. Часть была направлена в отдел контроля качества для проверки и анализа, но не было модели CAD части.
Кроме того, лазерное сканирование было так ново для организации, метода анализа данных без модели САПР еще не существовало. Новый метод измерения буквально должны были быть изобретены. Через много испытаний (и в основном ошибок), простой метод был разработан на основе базовой концепции, что основные решения процесс может быть смоделирован виртуально.
3-D сравнения образец сканирования. Его зеркальные сканирование быстро проиллюстрировать основной причиной производственных вопросов. Моделирование литейных процессов с 3-D лазер сканирует быстро рассматриваются вопросы обратной тяги (синий) в этом corebox. Анализ рабочего колеса проверка может показать области литья асимметрии, которые способствуют дисбалансу крыльчатки.
Для моделирования процесса, двух одинаковых сканирование corebox были ввезены в мощных компьютерных программ, одна проверка представляла corebox, а другие представляли песок само ядро. Сканирования были раздвигаются, чтобы представить стержневой оставив corebox. Мерных разница между этими двумя сканирования вычисляется и показано, как 3-D карта цветов. Обратный проект иллюстрирует, как отрицательная разница (синий). Этот опыт обучения показывает, способность видеть в сложных процессов и измерения сложных признаков вещественных частей, а не полагаться на идеализированной части САПР. Процесс сканирования, используя только данные развиваться и расширяться в течение последних нескольких лет, чтобы исследовать более сложные и разнообразные возможности улучшения процесса.
Улучшенный анализ баланса рабочего колеса Недавний проект с целью улучшения рабочего колеса баланса привело к разработке метода, который показывает особенности, которые способствуют дисбалансу крыльчатки. Основная идея метода основана на простой идее о том, что сбалансированная крыльчатка должна иметь ту же форму и форму, с одной стороны на другую. По сравнений по всей части, легко увидеть, если дисбаланс связан с изменениями в кастинге или обработка вопросов. Эта способность различать эти два атрибута не удалось до технологии сканирования. Общий метод был распространен на прямое сравнение отливки их отливки моделей, которые выделены различные возможности для улучшения процесса литья и дальнейшего сокращения рабочего колеса дисбаланс.
Сравнение симметрией частей Возможность сканирования в легко проверить симметрию сложных деталей, характерных деталей насосов был также использован в одном из недавних проектов по улучшению качества двойного корпуса всасывания. Образец подозреваемого литья был отсканирован и протестированы для симметрии. Данные сканирования было "зеркальным" в электронном виде, а затем проверяются на симметрии, сравнивая "левой руки" части картины его "правая рука" стороны. Один выявлению изображений показал, что каждая сторона картины была близка по форме к противоположной стороне, но расположение соответствующих частей не было правильным.
Эти несколько примеров показывают, как используя 3-D технологии лазерного сканирования на регулярной основе может постоянно улучшать качество, предлагая визуальные изменения сложных продуктов и процессов.
Об авторе: Роберт Килмер является продуктом техники для ITT Corporation, Goulds Pumps